What was originally planned as a simple cylinder head test on the 312 dyno mule ended up being a test that ultimately involved over two dozen different sets of cylinder heads. While part of this testing was a precursor to determining which pair of heads were to be used for an extensive exhaust system test, the remainder of the cylinder head test was to answer some questions about the significance of milling and porting on some of the various heads. This test saw no fewer than thirty different head changes on the engine as some of those pairs of heads were reworked differently between the tests or were reinstalled as part of the base-lining that was being performed to insure that the engine performance was remaining constant.
Where possible, the heads are tested with both the 1¾” stepped headers that were originally used on the 2009, 2010, and 2015 Engine Masters Challenge Y-Block engine entries and a set of 1½” four tube Sanderson pickup headers provided by Charley Burns (Thanks Charley). The Sanderson headers had an additional 22” of 2½” diameter collector extensions added to them. No mufflers were used on the Sanderson headers while the EMC headers used a set of 3½” inlet/outlet Magnaflow mufflers. Each set of headers had its own unique torque curve.
For this cylinder head test, this is the same +060 over 312 short block that has been used for many of the other dyno testing articles published in past issues of the Y-Block Magazine. As a refresher on the engine, the cast pistons are sitting 0.025” in the hole at TDC with a set of well used ECZ rods hanging from them. The camshaft is a Seventies era Crower Monarch grind with 280° advertised, 238°@0.0.50” and ground on a 110° lobe centerline. It is installed 2° advanced for this test or at 108° intake lobe centerline. The valves are put through their motions with a set of 1.6:1 Harland Sharp roller tipped rockers while a hot tappet lash of 0.019” is being maintained for all the tests. Lift at the valve after valve lash is 0.450”. The intake manifold being used for the cylinder head test is an unmodified ‘Mummert’ aluminum single four unit along with a 750cfm Holley vacuum secondary carb sitting atop a 2” dual oval carb spacer. The ignition chores are being taken care of with a MSD distributor and MSD 6A ignition box. Ignition timing was maintained at 38° total for all the tests while the harmonic damper is an Innovators West unit. The original oem damper had come apart in some previous testing which was replaced with the Innovators West unit.
I’ll add that at dyno pull #350 on this particular short block, a small lateral crack was observed in cylinder #8. Eight sets of heads had been run on the engine up to this point. Although there wasn’t any coolant leakage evident within the cylinder, it was definitely a crack and initial thoughts were to tear the engine down immediately upon finding the crack in the cylinder. Because it wasn’t known exactly when the crack did initially appear, I did decide to gamble and run the engine again with another set of cylinder heads. Four dyno pulls were made and with the heads again removed, the cylinder was re-examined. The crack didn’t grow so it was decided to just continue testing heads and examine the crack in detail each time the heads were removed. With the heads off the engine after dyno pull #365, that crack had grown significantly and the engine was then completely torn down so that cylinder number eight could be sleeved. There was still no water evident in the cylinder at this point but a fingernail could catch the crack as well as ring wear on one edge of the crack was now evident. The crack was now about 4” long traveling laterally at the upper part of the bore just below the deck. With a new cylinder sleeve installed, the engine was reassembled with the same rings and bearings; they all looked surprisingly good with only minimal wear showing. Upon starting up the engine and verifying that all is well, it is re-baselined. After confirming that it’s making the same HP & TQ numbers as before, the cylinder head test continued on.
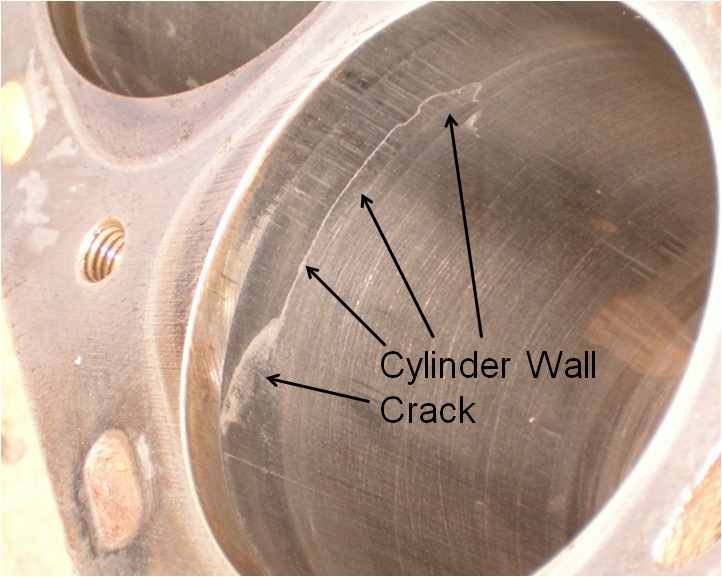
On the following page is a brief summary in chart form of how the various heads performed. A scoring format is used as this is a better indicator of how the cylinder heads perform over the whole rpm band rather than simply examining only the peak HP and TQ numbers. The scores are calculated by adding the average torque and horsepower values together, dividing by the cubic inches, and then multiplying by 1000. These particular scores are calculated where the ‘Engine Masters Challenge’ stepped headers are being used. Scoring with the Sanderson 1½” pickup headers will be included in part II of this article.
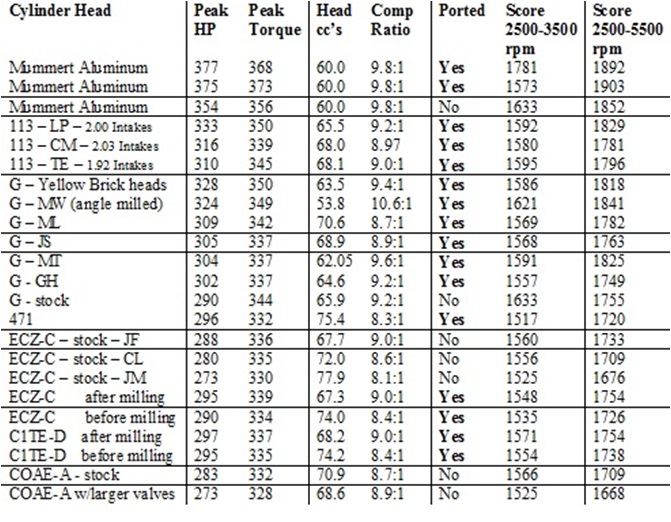
All the heads used for testing were cc’ed so that the differences in the compression ratios (C/R) could be taken into consideration. ‘Stock’ refers to the ports as delivered from the factory versus ‘ported’ meaning the intake and/or exhaust ports had some cleanup work or had been ground on. Any milling is represented in the combustion chamber volume as many of the heads were milled to some degree just to clean them up. The aluminum heads were used in their ‘as advertised’ 60cc format. The ported aluminum heads were far from being optimized on this particular short block but still managed to run away from the pack. 377 HP was impressive and the engine was buzzed up to 6400 rpms in order to do that particular evaluation. Many of the iron heads were out of breath by 5800 rpms or less.
Best Gasket head gaskets p/n 572G were used exclusively during this test. Issues with the Fel-Pro head gaskets leaking small amounts of coolant at the bottom of the heads in prior tests kept these particular gaskets from being used for this series of tests. During the cylinder head tests, different coatings or sprays were applied to the Best Gasket head gaskets to help facilitate cleanup between head changes. Although the use of silicone lubricant spray was a major improvement over using the gaskets without any thing added to them, the best results were achieved by using WD40 from a hand sprayer. Liberally coated with WD-40, the gaskets would pull off cleanly at the end of the test sessions and in two separate instances, the same head gaskets were used on five different sets of heads without any issues. While this
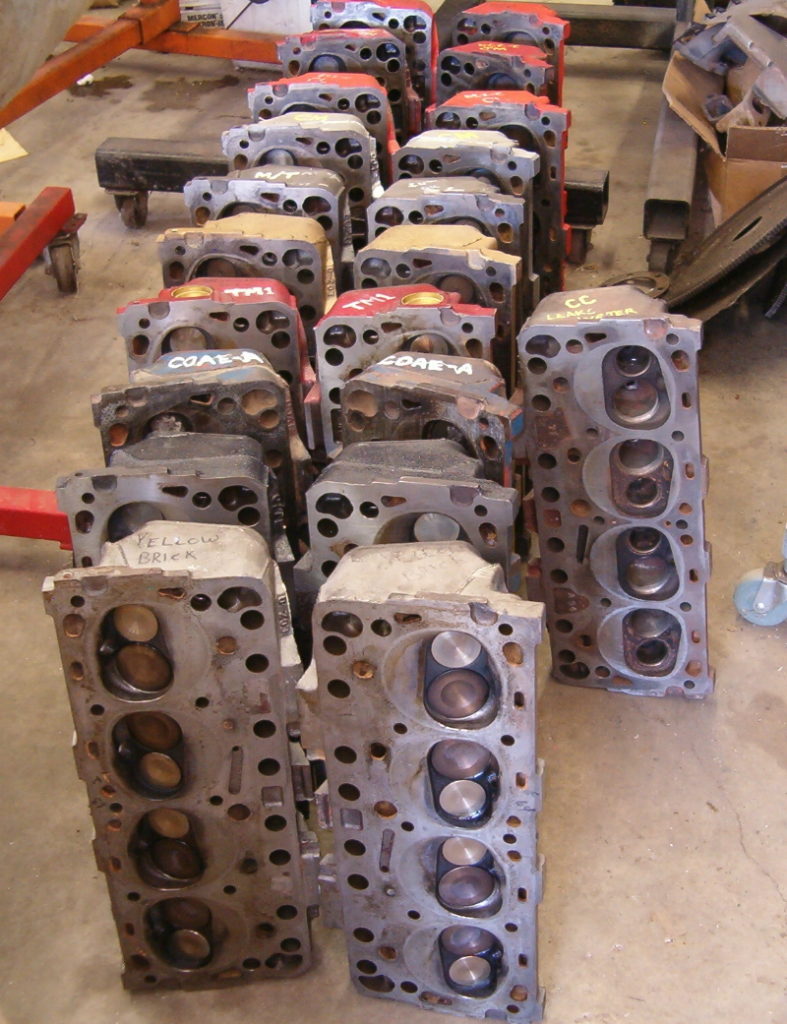
worked well for this particular dyno session, I would not recommend this as a common engine building practice without some additional info where real miles are put on the gaskets.
Both Best Gasket and Fel-Pro intake manifold gasket sets were used during this testing. While the Best Gasket intake sets sealed perfectly in their as supplied states, the Fel-Pro intake gasket sets were more conducive to being used repeatedly. The Best Gaskets would have a tendency to shred or come apart when the manifold was being removed. Spraying the intake manifold gaskets with WD-40 and then using white grease on the gaskets allowed the Fel-Pro intake gaskets to be removed cleanly from the heads and be reused. If the gaskets would survive that first intake change, then they would go on to survive several more intake manifold changes. As many as twelve intake changes have been made with the same set of Fel-Pro intake manifold gaskets with no adverse sealing effects being noted.
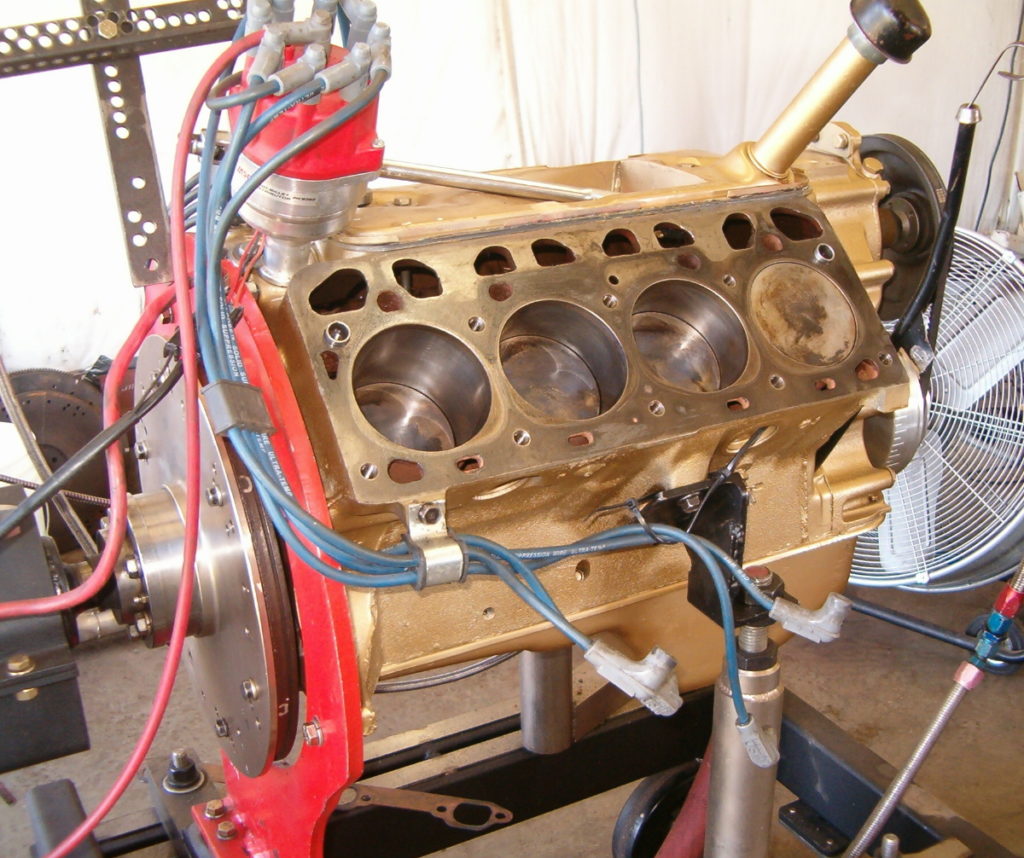
Also used during this test were the prototype ‘improved’ Best Gasket head gaskets that were sent for evaluation. The revised head gaskets are the same dimensionally but changes have been made to the composition material for improved sealing. There were no issues with the improved head gaskets. I’ll also mention that there was no re-torque of any the head gaskets being used after the initial warm up and again, zero problems. But I’ll add that ARP head bolts are being used which is a contributing factor to not having to re-torque the head bolts. A big “Thank You” goes out to Armin Brown and the rest of the crew at Best Gaskets for continuing to work on improving the gaskets for the Y.
Copper gaskets were used on the exhaust side of the heads and these were supplied by Relics Vintage Gaskets. Using the copper exhaust gaskets over a conventional fiber gasket minimized cleanup time between head changes while also helping to keep overhead costs for this test reasonable and to a small degree, at least under control.
Stay tuned as part II will go into more detail on the cylinder head test. Until then, happy Y motoring. Ted Eaton.
Originally published in The Y-Block Magazine, Issue #153, Jul-Aug 2019