A commonly asked question on the different internet forums has to do with the top end oiling problems that the Ford Y has been noted for over the years. Some of the answers are the result of years of misinformation and urban myths and have nothing to do with the actual reasons. And still other answers have to do with the disdain of this family of Ford engines and what the responder feels is the apparent need to swap the Ford Y out of the vehicle and replaced with anything else. But regardless, that top end oiling problem did and still does exist on some Ford Y engines. The occasional core engine does still show up here with those overhead oiling lines on it so that’s always a reminder that top end oiling issues are not only something that cropped up back in the day but is still with us today on the Ford Y family of engines. And I do still get the random call from someone with a freshly rebuilt or low mileage Ford Y that is not oiling at one or both of the rocker arms.
Here is the short list of probable causes for top end oiling issues.
- Rocker shaft orientation
- Improper cam bearing install
- Shallow camshaft journal groove
- Soft cam bearing babbitt
- Stopped up oil galley(s)
- Low oil pressure
- Cam journal groove is not aligned with oil feed hole
For freshly assembled engines that are not top end oiling, do not rule out the orientation of the rocker arm shafts on the cylinder heads. Even if using the overflow tubes on the rockers, it’s still a 50-50 chance of getting the orientation wrong if not paying attention. If making the shafts ‘pressurized’ and doing away with the overflow tubes, then there’s only a 1 in 4 chance of getting the orientation right if not paying attention. If using the overflow tubes, they will always be on the right side of the rocker assemblies, never on the left side. Oil will be exiting from those overflow tubes at the #1 and #8 cylinders. If not using the overflow tubes, then the rocker arm oil holes must be on the bottom of the shafts and a set screw or bolt will be required at the top of the far right side rocker arm pedestal (stand) to keep the shafts properly orientated so that the lower oil feed hole is always aligned with the corresponding oil supply hole at the cylinder head. The oil supply from the head is located at the second pedestal base from the right on both the head and the shaft. It’s important that the oil supply hole located at the bottom of the shaft is positioned so that it also aligns with the corresponding oil supply hole coming out of the top of the cylinder head.
Spun cam bearings are not on the list. While many of those early top end oil failures were blamed on spun cam bearings, that was not the case. Having literally pulled apart a huge number of these engines, none ever had a spun cam bearing; not the center cam bearing or otherwise. What I have found on some of these engines are center cam bearings that were simply installed incorrectly with only two of the three holes in the bearing being aligned with the holes in the block. When this is found, it has always been on engines that have been rebuilt and/or the cam bearings have been replaced. If the person installing the cam bearings does not know that there are three holes that must be aligned, then it’s quite easy for the center cam bearing to be installed with only two of the three holes being aligned. The two top end oiling holes residing at the center cam bearing hole are essentially hidden from easy view within the cam tunnel when the block is being prepared for the cam bearing installation. The person installing the bearings believes all is good when a cam bearing hole and the main bearing oil galley hole are aligned but that’s simply not the case. If the person installing the cam bearings is not familiar with this nuance, then the probability of the center cam bearing being installed incorrectly becomes a high probability. Murphy’s Law likely even increases the probability even higher in that if there is a way to do something wrong, then wrong it will be.
Another installation nuance is ensuring that the camshaft center journal groove aligns with the oil hole. If the cam bearing is installed either too shallow or too deep in its respective bore, then the cam journal groove either misses the oil hole or the oil flow is restricted even further depending upon the degree of misalignment. The wrong combination of camshaft retaining hardware at the front of the camshaft can also contribute to the cam groove not aligning with the oil feed hole. Using a light at the center main saddle hole before installing the crankshaft can verify that the camshaft journal groove is indeed aligned with the oil feed hole.
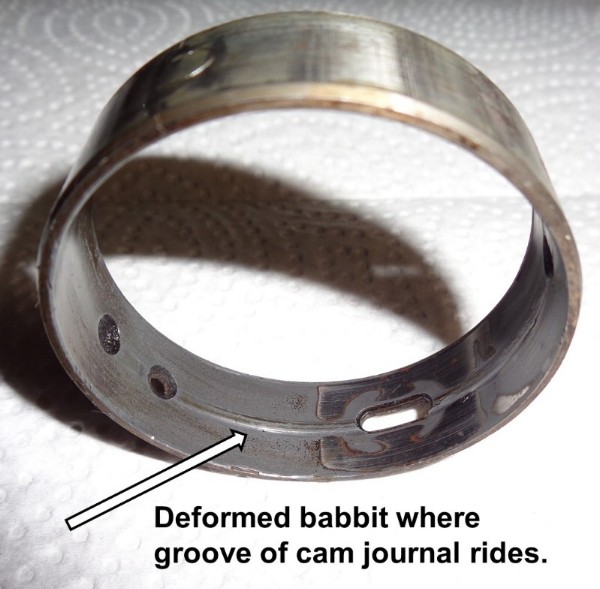
For both the original and rebuilt engines, there were and are other contributing factors though for the lack of top end oiling. One is the situation where the center cam bearing itself had worn to the point that the bearing material meshed into the camshaft groove thus shutting off the oil supply to the top end. Another is the stopping up of the top end oil galleys due to either infrequent oil changes and/or the use of paraffin based oils. The Ford Y when it was originally designed with the full flow oil filtration system was intended to be used with detergent based engine oils but many new car buyers simply opted to use the non-detergent oils they had already been using in their previous vehicles. Overheated bearings due to the lack of oil flow is also another reason for the lack of top end oiling. Also brought up on the various internet forums is milling the heads to the point that the oil slot in the head deck surface is taken down so far as to either restrict or remove the path for the top end oiling. I have never seen a head taken down so far as to cut off top end oiling. Those slots are in excess of 0.165” deep so that means the head deck surfaces would have to be machined at least 0.125” to affect the top end oiling. Even if composition head gasket swelling at that groove is thrown into the fray, it’s still going to be rare for top end oiling to be affected even if the heads are milled the aforementioned amount.
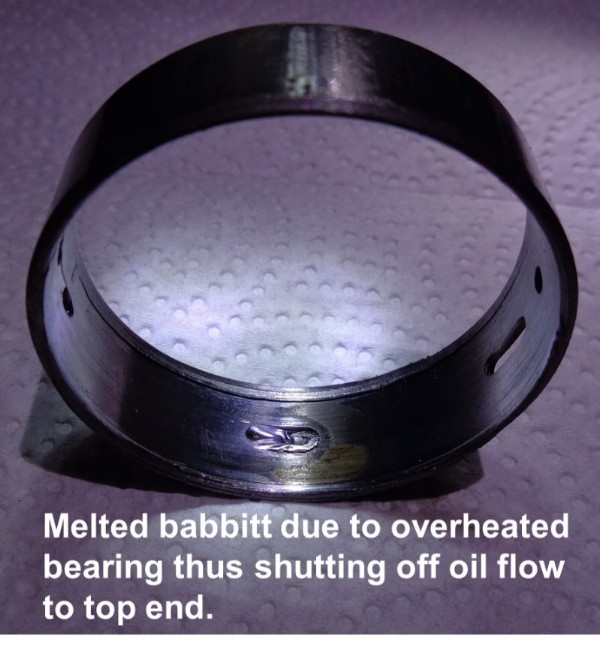
So that brings us back to the modern-day Ford Y builds where that pesky top end oiling problem still crops up today. First and foremost deals with the camshaft cores. For whatever reason, many cores come with a center oiling groove that is shallower than the original Ford specification. That makes any cam bearing babbitt deformation that takes place simply shutting off the oil supply to the top end much more quickly than would be observed if using a camshaft with a deeper groove. Second on the list is the modern crop of cam bearings. The Durabond, Melling, and Sealed Power bearings you buy today all have a softer babbitt material than what Ford originally used in the Ford Y’s. Those bearings have been known to fail in as little as 500 miles even when using stock valve spring pressures. When upping the valve spring pressures for high performance applications, those same cam bearings can fail even sooner as the babbitt material simply deforms even more quickly to squeeze into that center cam journal groove thus shutting off the oil supply to the top end. While those softer cam bearings are more easily modified for those engines that have cam tunnel alignment issues (312’s in particular), those bearings are more prone to the aforementioned deformation issues. The Engine Tech CC508 cam bearings made in South America on the other hand are a much harder bearing and not as susceptible to that same deformation as seen on those bearings made with a softer or more malleable babbitt. For the 272/292 engine builds, Engine Tech CC508 bearings are my go-to cam bearing set as those engines typically do not require much if any modifications for fitment. If doing a 312 engine, then the softer babbitt cam bearings are more desirable as those can be modified or cut on much more easily in which to have the camshaft to the point where it turns more freely. Regardless of the cam bearing set being used, it is highly recommended that additional work be performed either at the center cam journal or the block to ensure that adequate oil is supplied to the top end of the engine for the expected life of the engine.
While the oiling system for the Ford Y can be considered very good for main and rod bearing oiling, it is marginal for the top end. Part of that resides in the large size of the galleys going to the top end as the increased volume decreases the speed of the oil flow and subsequently allows for stoppages to take place. By design, the Ford Y had a designed oil restriction to the top end occurring at the cam journal itself. That reduced oil flow in conjunction with the larger than necessary oil galley sizing to the top end further increases the propensity for the stopping up of the oil galleys due to the very slow movement.
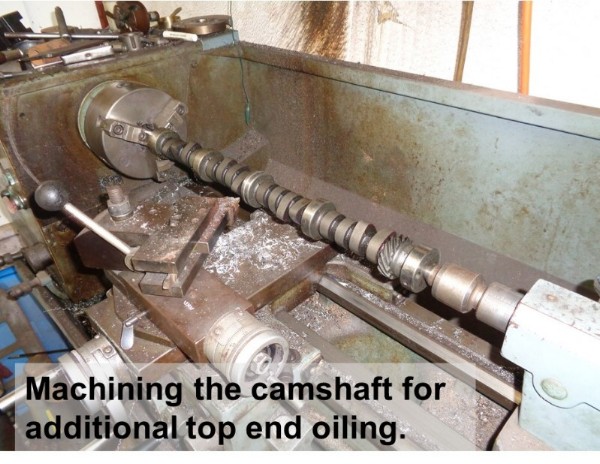
Modifications for top end oiling can include machining the groove in the center cam journal deeper, using a cam bearing with the oil groove on the outside of the bearing, or installing a groove in the center cam bearing hole that interconnects all three holes. The outside grooved cam bearing or putting a groove in the block circumvents the camshaft groove being relied upon to get oil to the top end of the engine. Machining the existing groove in the center journal of the camshaft deeper is relatively simple and easily performed by most machine shops. Using a cam bearing that has the oil groove on the outside diameter of the bearing is a special purchase item and care must be taken when installing that particular bearing as using a hammer and puck to install that center bearing can deform the bearing at its center simply making it too tight for the camshaft to fit in it when installing the cam. Those bearings are best installed using some kind of pull bar tool so that they are not shock loaded with a hammer and puck.
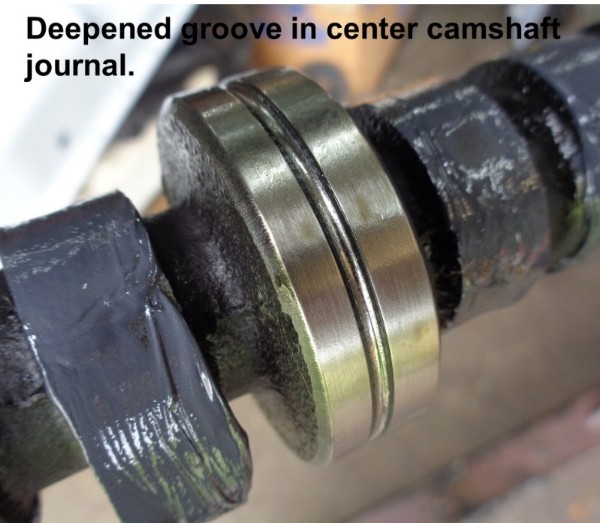
My own preferred fix is to simply put a groove in the center cam hole in the block that interconnects the three oil holes that reside there. The new bearing is then installed over the top of this new groove. While this operation has evolved into making a special tool to put that groove in the block, it was originally performed using an angle head die grinder with a thin grinding wheel and just carefully cutting the required groove into the center cam hole. The grooving operation performed in this manner is similar to what the Ford engineers did to provide top end oiling for the center oiling FE family of engines (352/390/428). I will add that the Ford 427 side oiler engines went to the grooved camshaft for top end oiling and those too had issues with bearing deformation shutting off the top end oiling. The 427 side oiler engines also benefit by machining the grooves in the #2 and #4 cam holes. By machining the Ford Y blocks with a groove in the center cam hole, those engines are fixed for the long haul including if the engine is torn down at a later date for another rebuild.
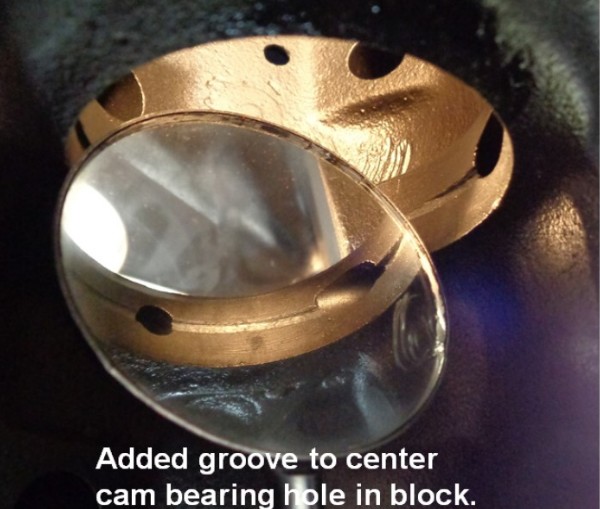
While the top end oiling is improved with any of the aforementioned modifications, the potential is there to have too much oil going to the rockers. This is alleviated by installing a restrictor at the bottom of the second from the right rocker arm stand. I have found that a 5/16-18 set screw drilled with a 0.078” orifice threaded into the bottom of the stand suffices for this. While not having enough oil flow to the top can be problematic, having too much is easily rectified with the use of restrictors.
Even with a good quality bearing set, it’s still important that the bearings be installed correctly. If not modifying the block for additional oiling, then it’s important for that center cam bearing to be installed with all three holes correctly aligned with the corresponding holes in the block. The number of Y engine cores that have come into this shop with an overhead oiler installed only on one side of the engine simply boggles the mind but all were a result of an improperly installed center cam bearing. Many of these overhead oilers were installed in lieu of pulling the engine back out of the vehicle and tearing it down to fix the improperly installed cam bearing. Overhead oilers were obviously a cheaper fix than pulling the engine back down and correcting the issue correctly.
As always, this information is simply intended to be ‘food for thought’ so just use it as best seen fit. Until next time, Ted Eaton.
Previously published in The Y-Block Magazine, Issue #166, Sep/Oct 2021.